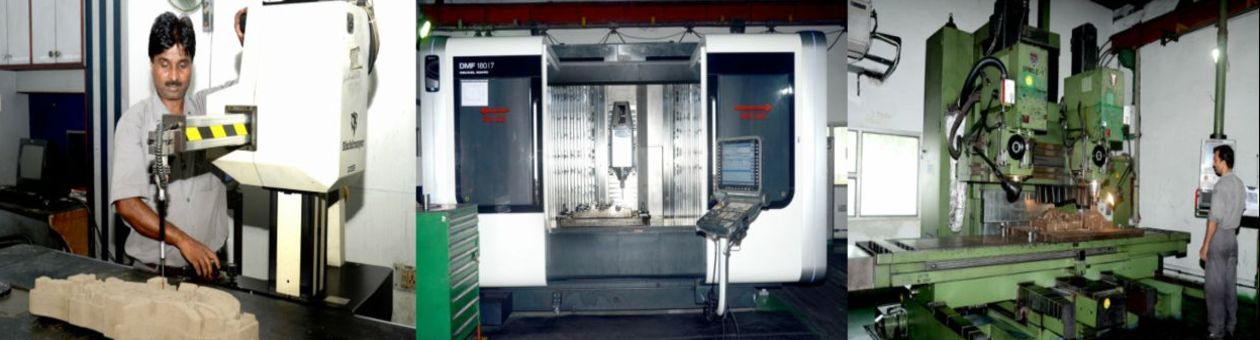
DCM Engineering has been an industrial front runner in the Indian sub continent. The history of DCM Engineering group goes back to 1889 with the Delhi Cloth Mills, when industry was in its infancy in India. Anticipating the tremendous boom in the automobile sector both nationally and internationally, the DCM Engineering Group setup a Grey Iron Foundry in 1977 with the capacity of 17000 MTPA as Division of DCM Engineering Limited. This was subsequently hived off as an independent company "DCM Engineering Limited” in 2004 (effective April 2001).
Capacity of this foundry was increased to 35,000 & 50,000 MTPA in the year 1994-95 & 2005-06 respectively. Recently, this capacity has been increased to 72,000 MTPA. This foundry is one of the leading foundries in India, in the segment of Automotive Castings. The foundry specializes in the manufacture of Cylinder Heads, Cylinder Blocks and Housings. The company has achieved the annual turnover level of INR 4100 million during the year 2012-13.
DCM Engineering is supplying castings across all segments in automotive market: Passenger Cars, Utility Vehicles, Tractors, Commercial Vehicles, Construction Equipment and Gensets. DCM Engineering is also exporting consistently for last 10 years. Its association with international customers includes General Motors and Perkins UK.
In domestic market DCM Engineering is associated with top automotive players: Maruti Suzuki India Ltd., Hyundai Motors, Mahindra & Mahindra, International Tractors Ltd., Ashok Leyland, Volvo Eicher Commercial Vehicles Ltd, Tata Cummins Ltd, Kirloskar Oil Engines Ltd., Suzuki Power Train India Ltd., Avtec Ltd., Escorts, SML Isuzu Ltd, JCB India, Force Motors, Man Trucks India Ltd., Greaves Cotton Ltd., Simpson & Co and many more.
DCM Engineering is now investing heavily in the latest Automatic Core Cell from Loramendi, Spain. Assembled cores will be the output of Auto Core Cell. This will result in castings with minimal weight variation from the Design weight, having highest level of dimensional accuracies, reduced core breakage and high productivity. Further parting line fins and Mismatch will be minimal thus reducing excessive fettling. DCM Engineering also invested in CNC Fettling Machines from Maus, Italy. With these machines the Blocks are getting fettled in-house with greatly reduced manual work content.
" At its Ropar plant company houses two high pressure moulding lines with press pour state of the art tooling & designing facility in addition to other supporting processes and equipments."
Company’s registered office is at New Delhi. It is a subsidiary of DCM Engineering Limited. DCM Engineering Limited is not a listed entity. Its holding company is however listed at BSE and NSE.
Research & Development Activities: Proto Development and validation of new products :
To understand the metal flow, mould filling, gases accumulation and solidification, MAGMA soft Simulation software is extensively used
DCM Engineering has in house Research and Development Centre for development of Proto Tooling, equipped with CNC machines (Vertical and Horizontal ) networked with Computer Aided Manufacturing (CAM).
DCM Engineering’s in house Proto Validation center is equipped with 3-D White Light Scanner (GOM- Germany). It consists of a topographic system working with 2 synchronised cameras to correctly & precisely capture 3D topography of the objects and can be compared with the 3-D Model.
We encourage the participation from our customers at various stages in the development process such as Product Design optimisation (DFM), Feasibility study, Value Engineering proposals for cost reduction and improvements in productivity.
A full-fledged Research and Development team with more than 200 years of cumulative experience in Foundry sector.